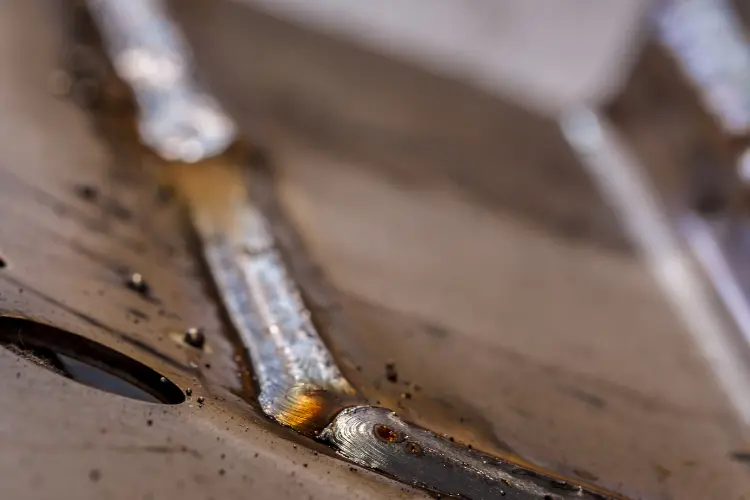
Thin metal sheets such as car panels need extra care for welding. Also, welding thin sheets is more difficult than welding thicker metals. And it becomes even harder with the MIG welder. Thus, many welders suggest novice welders bypass MIG welding for sheet metals at first.
But we are here with you with the best tips on welding sheet metal with a MIG welder. These tricks and tips would make MIG welding of thin sheets easy, smooth, and swift.
Thus, let’s get into the MIG welding techniques if you don’t want to ruin the entire process and the thin sheet metal.
Step-by-Step Guide on How To Weld Sheet Metal With MIG Welder
When you MIG weld any metal sheet, you must look at and care for two things.
- Burning through the sheet itself.
- Warping of the sheet, especially the edges
Creating excess heat and burning through one part of the sheet is easy. Even the most experienced welders find it hard to control the heat. It can only be achieved with patience and practice during the sheet metal welding process.
Choose the Right Electrode Wire:
It is essential to choose the right MIG electrode and wire for perfect sheet metal welding.
We suggest you select the wire with the smallest diameter. Since the wire has less diameter, it also takes less heat.
Hence, with less space, the wire will burn or melt the least space on the sheet. On top of it, an electrode with a smaller diameter allows you to recover any possible mistakes quickly. In this way, the small diameter electrode will cause the least warping and burn-through.
We talked with professionals in this regard. You should use 0.023 inches of wire for the MIG welding result. Also, choosing the right welder for beginners is important. You need to pick a versatile welder for MIG welding with infinite adjustability.
Preparing the Metal:
You must also prepare and clean the metal sheets before welding, especially with aluminum. Inspect the metal sheet and remove dust and dirt, if there are any. You may use a cleaning solvent or degreaser to remove the oil and dirt.
You may even use rust or oxidation remover to remove oxidation and rust. Last but not least, using a steel wire brush will help you to clean the metal sheet with the best results.
Choose the Right Setting:
You must rightly set the MIG welding parameters if you don’t want warping and burns on the sheet.
You must ensure the arc goes right into the welding puddle. Also, your hands must be steady so the weld doesn’t face weaving or whipping.
We suggest you choose the straight-line profile. Also, instead of holding the welder in the same place for too long, move it steadily and quickly from one end of the metal sheet to another end. It will prevent warping and offer a smooth bead profile.
Skip Welding Method:
Don’t worry; we aren’t recommending that you skip the entire MIG welding. ‘Skip welding’ is a welding technique.
It will allow you to distribute the heat through the electrode evenly.
- The process refers to creating a weld hole first, then skin a few inches for the next weld hole.
- You need to continue the process until it reaches the end of the metal sheet.
- For instance, if you work with a 2-feet by 2-feet steel metal sheet with an 18-gauge thickness, create a 1-inch puddle or hole first.
- Then, skip 6 inches and make the next hole until you reach the end.
- Then, repeat the process from that end.
- But this time, create the puddles in every 3-inch distance.
- As you repeat the process, it helps in even welding with proper heat distribution.
Use Bars as Backing:
When you weld a particular portion of the sheet metal, the heat must dissipate as quickly as possible from the metal. It will prevent burns and warping of the metal sheet. We recommend you use a backing bar for this purpose.
The backing bar is commonly made of aluminum or copper. The bar will be clamped with the welding piece base and will help dissipate the heat quicker and better. You may even choose the backing bar with a water-cooled function for heavy-duty MIG cycles.
Joint and Fit-Up:
You must fit and joint the thin sheet metal piece with all the welding pieces as tightly as possible. The joins must be tight and well-fitted. If there is a gap between the two welding materials, the weld will be poor quality.
Hence, when cutting the metal sheet for welding, you must measure its accuracy several times. Also, make sure that the fit is top-class.
Tips and Tricks for MIG Welding Sheet Metal
- A MIG welder with infinite adjustability will be the best option for welding thin metal sheets. Also, a multi-purpose welder will allow you to adjust the settings to meet the requirements and match your desires. You can adjust the voltage and wire feed configuration as well.
- There’s nothing better than your experience for the best MIG welding output. Thus, we suggest you practice MIG welding as much as possible. You may try different configurations and see which works best for what metal and thickness. You can use scrap metals to practice and develop your MIG welding skills.
- Using thinner electrode wire will surely result in better welding output. We have already discussed that using 0.023-inch electrode wire will yield the best welding results.
- Many welders use a long bead to weld thin metals. It runs the risk of burning the sheet more. So, we suggest you use a short burst of weld quickly. It permits to have better control over the entire welding process.
Final Words
MIG welding is challenging, mainly when working with a thin metal sheet. We hope this guideline, including different tips on welding sheet metal with a MIG welder, helps you achieve the best results.
Nonetheless, you must never forget that MIG welding is all about practice, practice, and practice. The more experience you have, the better the MIG welding result.
Leave a Reply