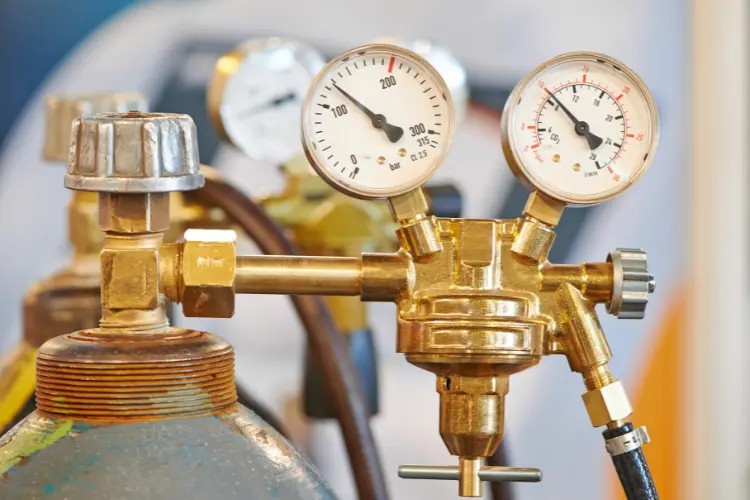
Welding is the process of joining two pieces of materials, such as thermoplastics or metal, using high heat levels. The melted parts are then left to cool to form a joint. Apart from electricity, some gases are often operating in the welding process.
Gases are often used to shield the area which needs to be welded. This is because some gases in the air alter the way they weld. The type of gas used will inevitably determine the welding process to be used.
Some common gases used in welding are acetylene gas, argon, oxygen, and even air, among others.
Noted: In welding processes, certain atmospheric gases like nitrogen and water vapor are generally not used as shielding gases because they can cause weld defects and oxidation.
6 Types of Gases Used In Welding
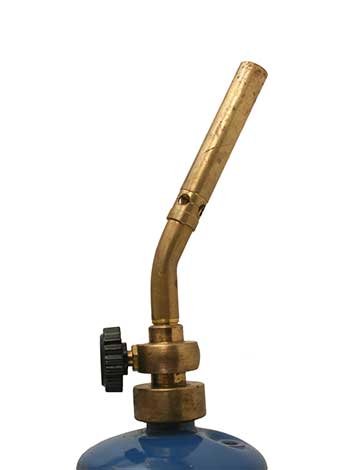
Gas Type | Short Summary |
---|---|
Argon Gas (Noble shield) | Argon gas is used in TIG and MIG welding as a shielding gas to prevent oxidation and contamination. |
Oxygen (Heat booster) | Oxygen gas is generally mixed with other gases to boost the welding process by aiding the combustion of the welding arc. |
Acetylene Gas (OG flamethrower) | Acetylene Gas is flammable and commonly used in welding and cutting processes, producing a high-temperature flame when burned with oxygen. |
Carbon Dioxide (Fizzy flux) | A reactive gas that can be used alone or mixed with argon in MIG welding. |
Helium (Speed demon) | An inert gas often mixed with argon to improve weld quality. |
Hydrogen (Invisible helper) | Hydrogen improves welding properties, like cleaner welds, with less oxidation when added in small amounts to argon or other gases. |
1. Argon Gas
Argon is a gas that is nonflammable, nontoxic, and inert. This means that it does not react chemically with other materials or even metals.
Argon is often used in the manufacture of steel, heat treatments, and even the manufacture of electronics.
In other circumstances, argon is often blended with Hydrogen, carbon dioxide, or oxygen to enhance the character of the arc produced during the welding process.
Since it provides a stable arc, it is an ideal shielding gas used with different types of metals, such as titanium.
Argon is costlier than other shielding gases and welding operations, especially for large-scale projects. Its high density compared to air makes it challenging to use in vertical or overhead welding applications, leading to practical difficulties in ensuring consistent shielding.
2. Oxygen
Oxygen is one of the most popular gases known, which makes combustion possible and also supports life. It is a colorless, tasteless, and odorless gas.
This gas often works with other types of gases that are necessary for the welding process. Therefore, using oxygen when using high heat on metals is necessary.
Oxygen is also known to promote arc stability and, at the same time, reduce the surface tension that may be exerted on the molten metal.
This increases the wetting of the metal. On the other hand, excessive gas application can lead to the area's brittleness exposed to heat.
The primary drawback of using oxygen in welding is its high reactivity, which can lead to oxidation and weakening of the weld.
3. Acetylene Gas
Acetylene is a colorless and highly flammable gas that is considered the hottest of all hydrocarbon gases. It is widely used for brazing, cutting, and welding steel alloys less than 1 inch thick. Acetylene has many favorable features, such as producing a gas mixture that reaches a higher temperature than other gases. Additionally, it can easily switch into a cutting process by changing the welding tip to a cutting tip.
However, acetylene is unstable and can become explosive under high pressure. Therefore, it needs to be handled and stored with great care. Moreover, it has a narrow flammability range, which poses additional risks if not adequately regulated. If not correctly combusted, it produces a sooty flame that can contaminate the weld area. Finally, acetylene is more expensive than other fuel gases like propane, making it less economical for some applications.
4. Carbon Dioxide
Carbon dioxide is also one of the popular reactive gases used in welding, which is tasteless, non-flammable, odorless, and colorless gas. It is also considered the least expensive shielding gas.
Although the gas is known to have drawbacks, it is also known to have many advantages. In cases where thick material needs welding, carbon dioxide is often preferred, and this is because it promotes deeper penetration of the weld.
In addition, carbon dioxide does not require an additional inert gas for it to be used.
5. Helium
Helium is also another standard gas used in welding. Apart from the fact that helium gas is colorless, odorless, and tasteless, it is also considered one of the lightest gas elements besides Hydrogen.
Helium can be mixed with carbon dioxide and argon to weld stainless steel. It has several favorable properties, such as producing a wide and deep penetration, making it ideal for thick pieces of metal.
However, due to its low density, it can be difficult to use in positions other than flat or horizontal, as it can easily disperse and fail to provide adequate shielding.
Also, initiating the welding arc can be more challenging with helium because of its higher ionization potential. This may require higher flow rates, increasing its cost and usage.
6. Hydrogen
Hydrogen is known to be the lightest gas element. It is a colorless, odorless, and tasteless gas. In welding, using Hydrogen can increase the arc temperature, resulting in better penetration during the welding process. Hydrogen can combine with argon and carbon dioxide to counteract the oxidization effects caused by exposure to carbon dioxide.
However, the application of Hydrogen gas is usually limited to certain types of stainless steel.
It is essential to note that Hydrogen is highly flammable and explosive, so strict safety measures are necessary to prevent accidents.
Conclusion
The above gases are the most common gas elements used in welding. Therefore, it is important to consider some factors to use a specific type of gas to weld. Such factors include the type of metal being used and, at the same time, the degree of temperature that the gas can produce for the welding process to become effective.
Therefore, it is paramount to consider the compatibility of the gases with the different types of metals.
Leave a Reply